MERGE
Contact and tied interfaces
"Optional title"
coid
entype${}_s$, enid${}_s$, entype${}_m$, enid${}_m$, $tol$, mfid, gid, penalty, $\alpha_{max}$, no_self
Parameter definition
Description
This command can be used to merge disjointed meshes. Note that the finer element grid should be on the slave side. Interface forces are written to merge.out. Maximum tensile and shear stresses are also output, if a failure criterion has been define (parameter mfid). Symmetric (two-way) merge is possible, but it should not be combined with a cohesive failure criterion.
The command generates a file _node_merge_project.k containing INITIAL_DISPLACEMENT projection vectors for all merged slave nodes. The INITIAL_DISPLACEMENT commands can be used to adjust the slave node positions, to be located right on the master faces.
Note SPH sub-domains must be on the slave side when merged with finite element surfaces.
Example
Merge disjointed meshes
A flexible pipe with part ID = 10 is merged to a plate with part ID = 20. The pipe is given an initial velocity of $100 \mathrm{m/s}$. The rigid plate is fixed in space.
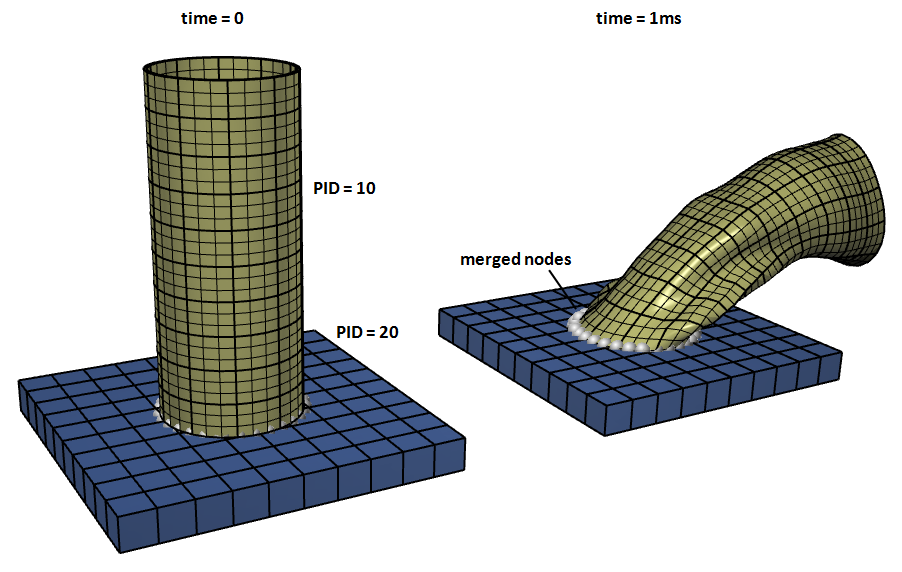
Merge with initial displacements
A pipe (slave entity) is merged to a box (master entity).
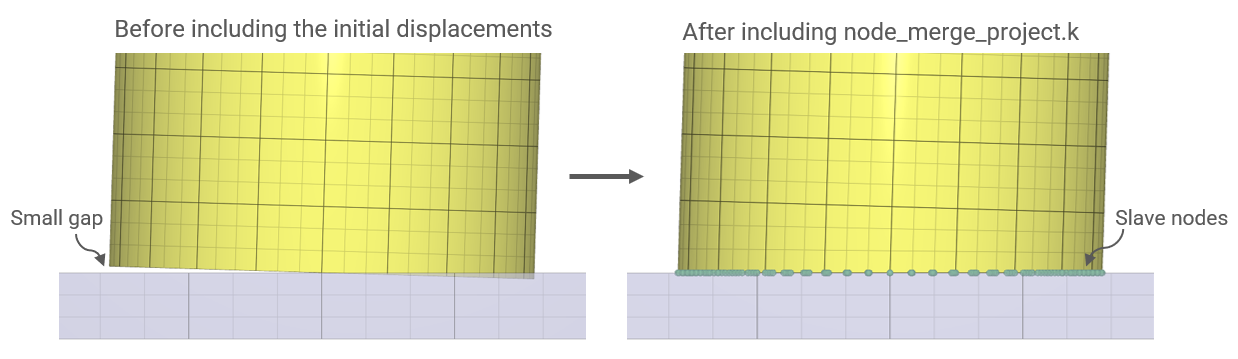
The file _node_merge_project.k is automatically generated when starting the simulation. It is then included to the main file. The node positions of the slave nodes are adjusted with the help of the initial displacements within the included file when rerun. Note that the file name is changed to node_merge_project.k in the example.
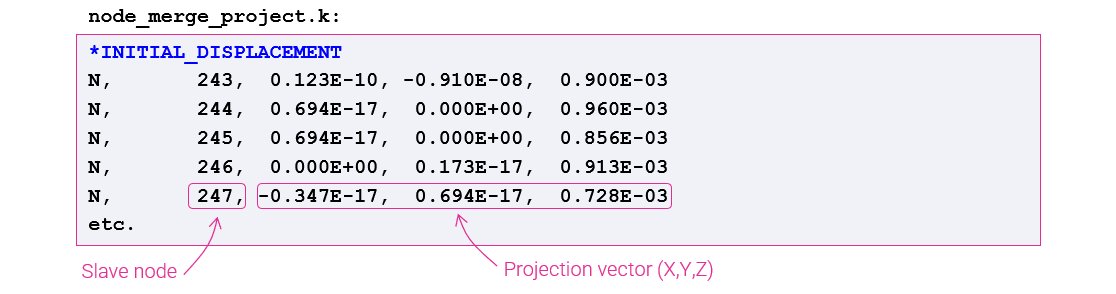