OUTPUT_SENSOR_THICKNESS
Output
"Optional title"
coid, pid, $x_0$, $y_0$, $z_0$, fixed, $t_{beg}$, $t_{end}$
$n_x$, $n_y$, $n_z$
Parameter definition
Description
This command is used to sample the thickness of a part at a given location or material point. The measured thickness is written to sensor_thickness.out. In FUNCTION the thickess can be accessed through thicks(coid).
The vector defining the the thickness measuring direction is optional. It only needs to be specified in situations where the nearest point on the external surface is not defining the thickness direction. The example below shows such a situation. As the workpiece moves forward in positive x-direction, the sensor first reaches the front face of the workpiece. This face does not represent the thickness direction and it should therefore not be used in the measurement. Hence, it is necessary to manually define a vector, in this specific case $(n_x,n_y,n_z)=(0,0,1)$ .
Example
Adjust vertical position of rolls using a thickness sensor
A complete model of a rolling process. The vertical motion of the rolls is adjusted to reach a target thickness of the workpiece.
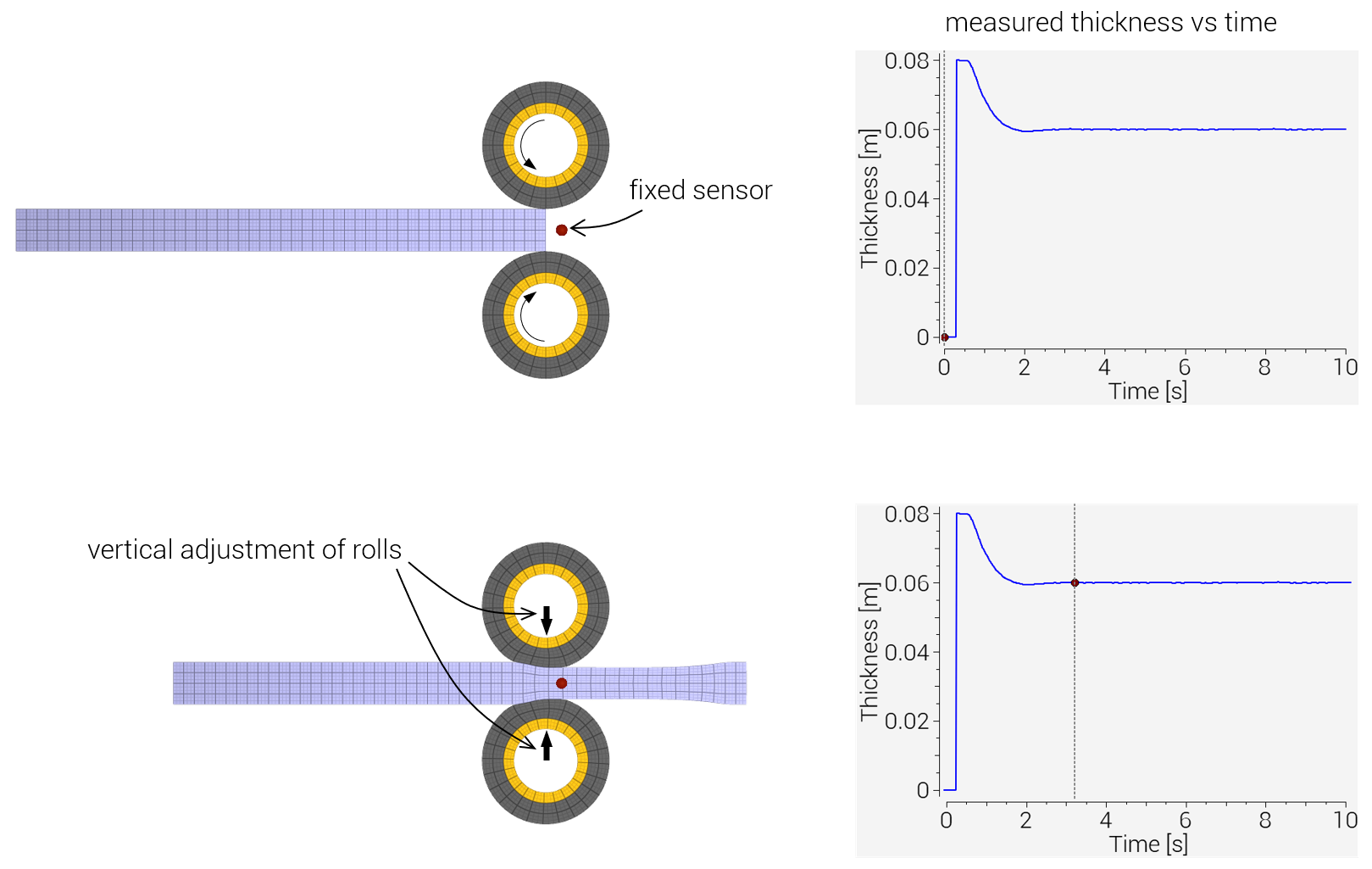
Command file:
Python script rolls.py:
#
# SET VERTICAL ROLL VELOCITY TO REACH TARGET THICKNESS
# h_actual = current thickness at sensor
# h_target = target thickness at sensor
#
def adjust(h_actual, h_target):
if (h_actual > 0):
vertical_velocity = h_actual - h_target
else:
vertical_velocity = 0
return vertical_velocity