TRIM
Mesh commands
*TRIM
entype, enid, nid${}_{seed}$, $t_{trim}$, $\hat{x}$, $\hat{y}$, $\hat{z}$
$x_1$, $y_1$, $z_1$
.
$x_n$, $y_n$, $z_n$
entype, enid, nid${}_{seed}$, $t_{trim}$, $\hat{x}$, $\hat{y}$, $\hat{z}$
$x_1$, $y_1$, $z_1$
.
$x_n$, $y_n$, $z_n$
Parameter definition
Variable
Description
entype
Entity type
enid
Entity ID
nid${}_{seed}$
Seed node id, marking material to keep after trimming
$t_{trim}$
Trim time
$\hat{x}$
X-component of trimline projection direction
$\hat{y}$
Y-component of trimline projection direction
$\hat{z}$
Z-component of trimline projection direction
$x_1$
X-coordinate of trim line point 1
$y_1$
Y-coordinate of trim line point 1
$z_1$
Z-coordinate of trim line point 1
.
$x_n$
X-coordinate of trim line point $n$
$y_n$
Y-coordinate of trim line point $n$
$z_n$
Z-coordinate of trim line point $n$
Description
Trimming function for metal stamping applications. The trim path is a discretized line, defined by a list of coordinates. The command is only compatible with third order elements.
Example
Trim 1
The following command defines a trimming operation on part 4 at time 0.2. The seed node 88460 marks the material to keep after trimming. The trim line is projected on the metal sheet in the z-direction.
*TRIM
P, 4, 88460, 0.2, 0.0, 0.0, 1.0
-0.681E+03, -0.235E+03, 0.468E+02
.
-0.683E+03, -0.249E+03, 0.371E+02
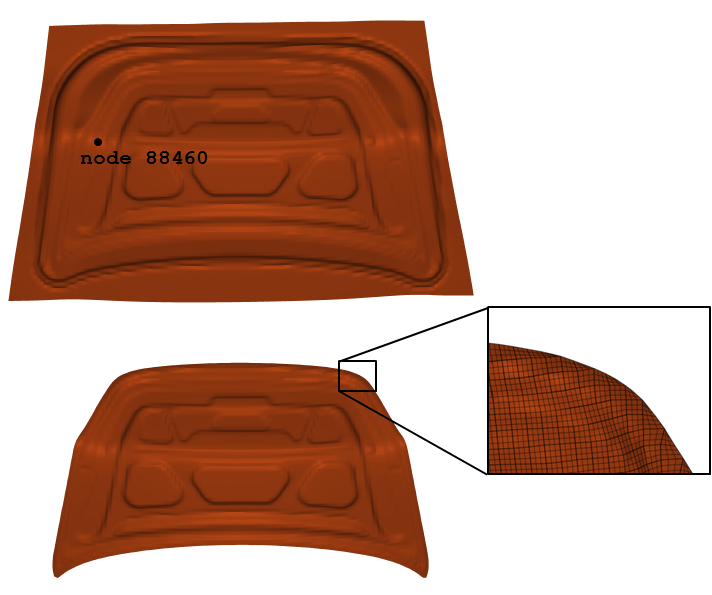
Trim 2
For lancing operation where there is no scrap material, the seed node is to be omitted. The example below is a lancing operation on part 3 at time 0.01. The cutting line is projected on the metal sheet in the z-direction.
*TRIM
P, 3, 0, 0.01, 0.0, 0.0, 1.0
-13.6, 10.2, 0.0
10.3, -12.2, 0.0
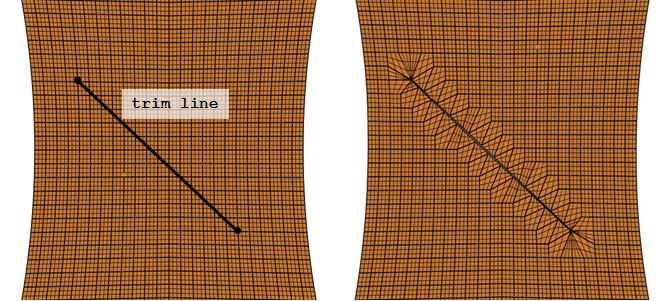